
ELECTRIC PORSCHE 356 KIT
Spec sheet
Model | 1961 Porsche 356 B T5 Cabriolet | Brakes |
Uprated CSP disc brakes
Regenerative braking
|
Colour | Aetna Blue | Suspension | IRS with uprated, adjustable SPAX shocks |
Interior | Announcement coming soon | Weight |
920kg
Distributed 60/40 rearward, as per stock
|
Drivetrain |
Direct drive EV with bespoke rear subframe
450 volt system
100kW peak, 320N.m AC Motor
20.7kWh traction battery
Single 5.2:1 ratio reduction gearbox
CCS2 DC ultra-fast charging
|
Comfort |
Wireless Apple CarPlay / Android Auto
Modern sound system
Full sound deadening and insulation
Period sensitive modern LED lighting
Electric power steering and collapsible steering column
Cabin heating / air conditioning coming soon
Sport/eco driving modes coming soon
|
Model | 1961 Porsche 356 B T5 Cabriolet |
Colour | Aetna Blue |
Interior | Announcement coming soon |
Drivetrain |
Direct drive EV with bespoke rear subframe
450 volt system
150kW peak, 320N.m AC Motor
20.7kWh traction battery
Single 5.2:1 ratio reduction gearbox
CCS2 DC ultra-fast charging
|
Brakes |
Uprated CSP disc brakes
Regenerative braking
|
Suspension | IRS with uprated, adjustable SPAX shocks |
Weight |
920kg
Distributed 60/40 rearward, as per stock
|
Comfort |
Wireless Apple CarPlay / Android Auto
Modern sound system
Full sound deadening and insulation
Period sensitive modern LED lighting
Cabin heating / air conditioning coming soon
Power steering and collapsible steering column coming soon
Sport/eco driving modes coming soon
|
A vehicle fit for purpose
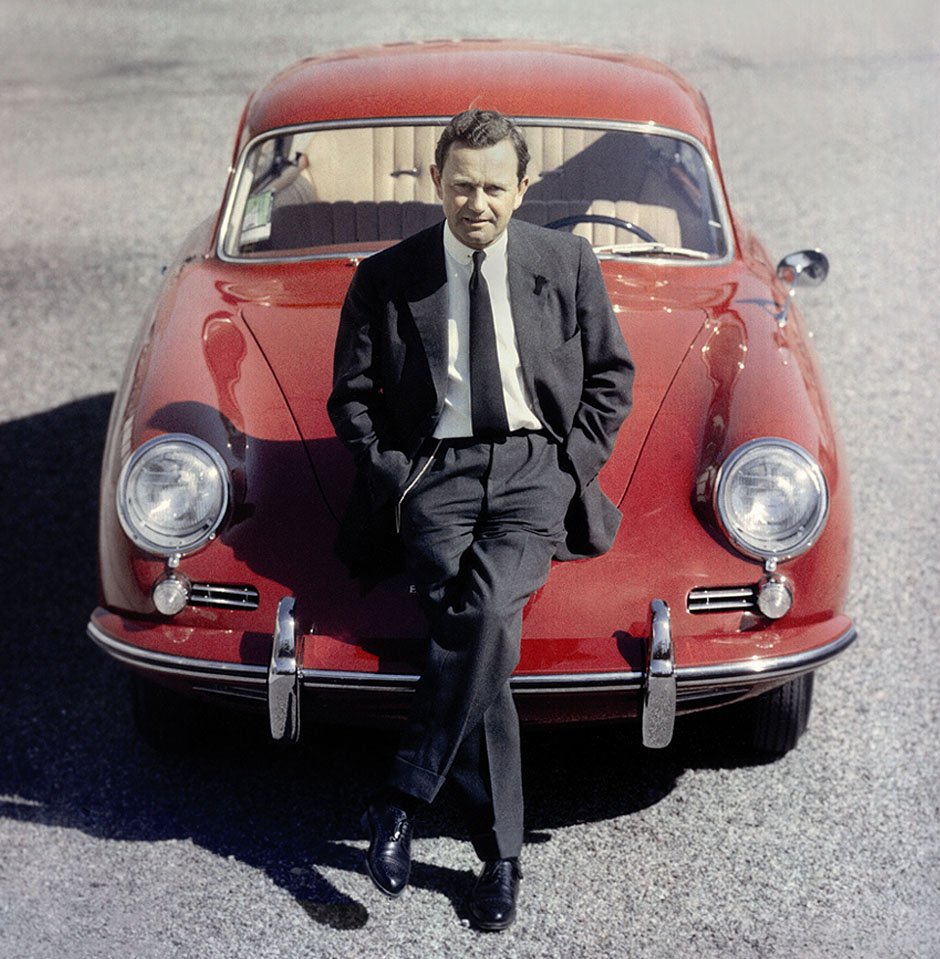
The 356 was the first vehicle to bear the Porsche name, with the first rolling off the production line in 1954.
The seed for the 356 was sown over 15 years earlier, while Ferdinand Porsche and his son Ferry (adjacent) were cutting their teeth as young engineers working for the German government on a bold, new project to design a reliable, efficient “people’s car”. Yes, that one.
Although some of the Beetle shape undeniably carried into the 356, the biggest carry over was the philosophy and focus on designing vehicles that are uncompromisingly fit for a purpose. For the Beetle, this was reliability, efficiency and mass manufacturability. For the 356, this was to race.
Build quality, engineering simplicity and design that's fit for purpose is at the heart of the modern Porsche empire. It was the 356 that laid these foundations 70 years ago.
Our car: a humble, solid foundation
This specific 356 was delivered to Alfred Schmid of Munich, Germany in February 1961. Alfred spec’d a convertible with removable hardtop (rare), Aetna blue paint, a light grey leather interior and chrome wheels.
The 356’s Kardex, including options, dates and warranty servicing
Over time, we believe it made its way from Germany to the US, before jetting to Adelaide where it was stripped and converted to right hand drive with ambitions of becoming a modified “Outlaw” 356, before ultimately making its way to a Melbourne collector.
By the time we found the car, it’d certainly had a life. Over the years, the original Aetna blue paint had made way for white, and then matte grey. The engine had long disappeared, and some body restoration had been undertaken, presumably due to rust. The car was complete, but rough, and mostly in boxes.
Although daunting, the more we stared at it, the more we realized how solid the foundations really were, and how spectacular it could be as a re-imagined modern EV.
With the car shipped up to Sydney, we started by unwrapping the window glass from layers of patinaed newspaper featuring the imminent fall of the Berlin Wall plastered over the front page. This car had been out of action a very long time. It was time to get it back on the road.
Planning the electrification
The first order of business was to plan the electric drivetrain.
We set some ground rules, which apply to any electric conversion we undertake:
Direct drive: the gearbox of a 60+ year old vehicle isn’t designed for the torque profile of a modern electric motor. Maintaining an original gearbox as part of an electric drivetrain comes with significant reliability compromises that we are not willing to make. Ask us how we know.
Off-the-shelf: we would only use new, warrantied components. No salvaged parts from crashed electric vehicles.
High voltage: the traction packs must run at 350V or more, for compatibility with ultra-fast charging networks and to allow use of compact, high gauge wiring throughout.
We connected with Anthony Abbot of Halley Abbot in Buckinghamshire, UK. The Abbot family is a dynasty of Porsche expertise, and Anthony comes from years of high-tech design experience as a senior engineer with championship-winning Mercedes and Red Bull Racing Formula One teams.
Anthony had been dreaming of designing a scalable direct-drive electric conversion platform, and was seeking to collaborate on a 356 conversion. It was clear we were highly aligned in our engineering principles, and agreed to put our heads together and get to work.
The world's first direct-drive 356
There was significant trailblazing in this plan.
Although more robust, direct-drive EV conversions are significantly more complex than bolting an electric motor to an original gearbox. There are less than a handful of electric 356 conversions in the world, and none of them are direct drive. This was going to be a world first.
Note: the unused gearbox out of our car is to be donated to another 356 EV which has recently broken its own. Thank you for your noble sacrifice.
The 356 also presents substantial packaging challenges. Compared to e.g. the large, boxy layout of a body-on-chassis Land Rover, the 356 has a body of complex, compound curves wrapping a compact, monocoque chassis. Squeezing everything into such a small irregular space was going to involve a lot of head scratching.
Before we got too ahead of ourselves, our first challenge was geographical and logistical. it was the middle of a global pandemic, we were with our car in Sydney, Halley Abbot was in central England, and the fabrication team was in Johannesburg, South Africa.
A cross-continental electric endeavour
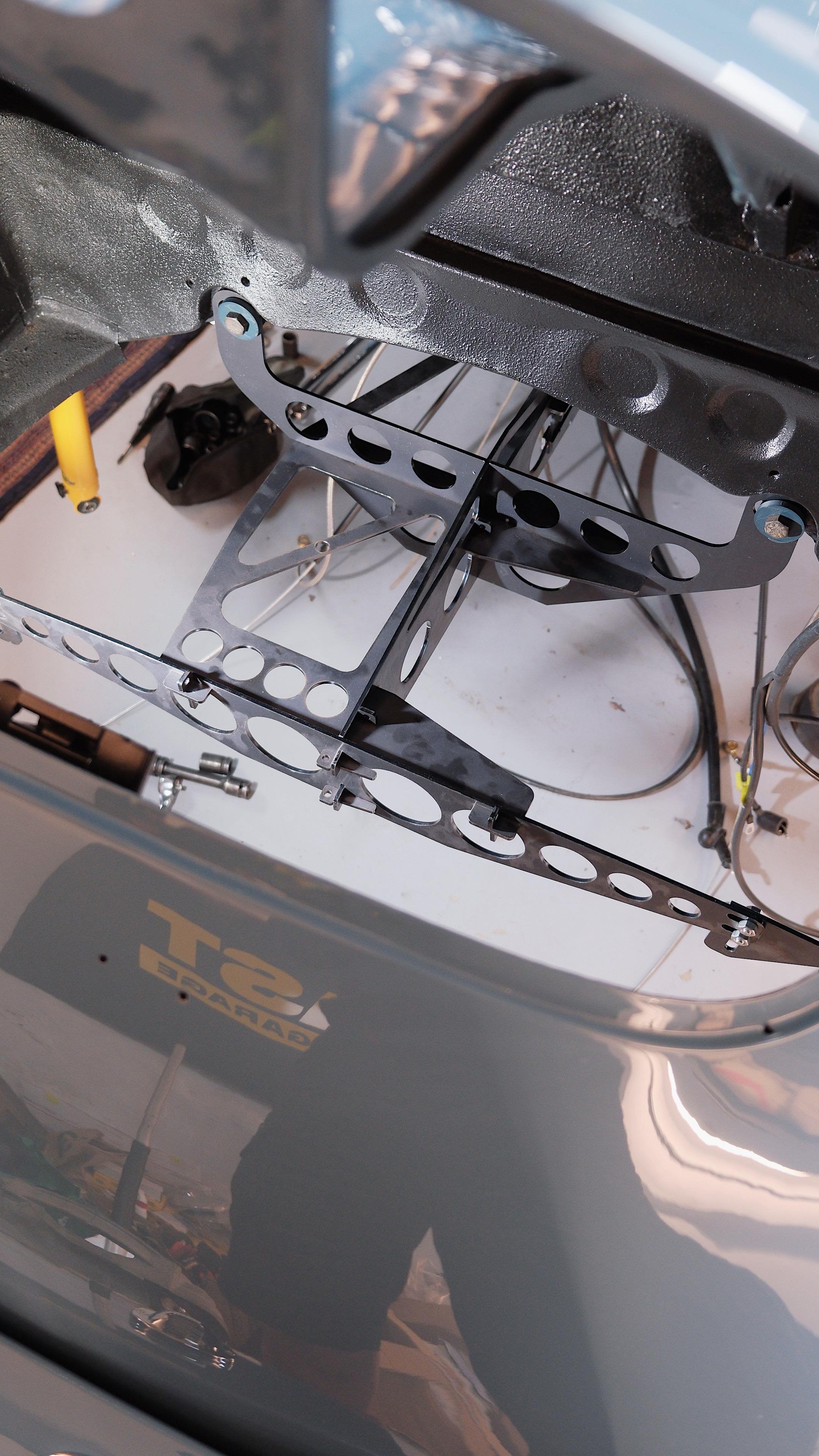
With the car needing a full nut-and-bolt restoration on home soil, there was no option to ship the car to Halley Abbot in the UK to aid development of the EV drivetrain (and have the project done this side of 2030). We had to get smart and parallelize efforts.
Fortunately, the last 5-10 years have brought modern prototyping techniques such as 3D scanning and printing rapidly down the cost curve and rapidly up the quality curve. By scanning a vehicle, and reverse engineering the generated 3D mesh into a discrete CAD model, complex components can be designed quickly and cheaply from an office or café anywhere on the planet.
Going one step further, after 3D scanning our vehicle in Australia, the teams at Halley Abbot scanned a handful of other loaner 356s in the UK and South Africa. This allowed us to establish what tolerances and adjustability should be built into the electrification design such that future conversion kits could be built from the same plans and “bolt straight in” to other 356’s without modification. Remember, these cars were hand built. Porsche did a remarkable job of building 78,000 almost identical 356’s, but the reality is they all have minor dimensional differences.
Jumping into the virtual world, a bespoke subframe was designed in CAD to reversibly bolt into the original engine/transaxle mounts and hold the batteries, electrical components, motor, gearbox and differential in place. Although designed in the UK, 20,000km away from the physical car, we were fairly confident the subframe would “bolt right up” in the real world. That said, best be safe. It would be immensely disappointing to assemble and ship everything halfway around the world for it to not quite fit right. For all the smart stuff, there really is no substitute for holding metal up to a car.
As a sanity check, a jig (see adjacent) was CAD designed comprising 3D printed plastic and laser cut steel pieces that clicked together as if from a certain Swedish furniture brand. Sent digitally and constructed locally, this was a cheap and quick solution to give us complete confidence that the EV subframe would line up with the stock mounting points. Truly a testament to how accessible and powerful low-volume prototyping has become.
To add one last piece of geographical complexity, the design for the subframe and suspension components were then sent down to Halley Abbot’s crack fabrication team in Johannesburg, South Africa. This steel work is currently being shipped directly from South Africa to Sydney for fitment, in advance of the remainder of the drivetrain being sent separately from the UK.
Needless to say, we all now know a lot more about global logistics than we ever anticipated.
The restoration and re-imagination
Meanwhile, on home soil, we launched into the vehicle restoration. The plan was to (mostly) return the car to factory spec as optioned by Mr. Schmid in 1961. This meant Aetna Blue paint, light grey carpets, chrome wheels, leather interior and a matching, removable hard top. Thanks to Mr. Schmid’s impeccable taste, this stunning combination of options made the decision to go back to stock very easy.
Every square centimeter of the car required some form of restoration, with us opting to reuse original parts where possible. All chrome pieces were removed for re-plating and all aluminum pieces were removed for polishing.
The original wiring harness was in a very dire state, so was removed and replaced with a new loom from Kroon. If the car were to catch fire due to an electrical short-circuit in the original harness, after going to all the effort to install a new cutting-edge electric drivetrain, the irony would probably kill us. While we were there, we updated all electrical components from 6V to 12V.
The interior is currently being lined with modern sound-deadener and thermal insulation before the interior trim is installed. You may think this is overkill for an EV, but you don’t realise how annoying the sound of pebbles flicking into your wheel arches are until you don’t have an engine to drown them out.
All stock bulbs have been replaced with modern LED equivalents for safety, longevity and efficiency. We’re very particular about choosing period sensitive low kelvin bulbs.
A smattering of comfort features will be installed once the interior is fitted, including a ripping sound system with Bluetooth connectivity and wireless Apple CarPlay/Android Auto. We have designs for additional creature comforts, including air conditioning/cabin heating and power steering. Watch this space.
Finally, as the pièce de résistance, a bespoke ELECTRIC badge was water jet cut from solid brass to match the original rear PORSCHE badge.
Next steps and future projects
We are immensely proud of this project and are truly grateful for the friendships and connections we built along the journey.
That said, the story does not end with this car on the road. The engineering foundations for many more future projects have been laid by this project, and it will continue to be used as a prototype and proving ground for further R&D.
To this end, we have major additions and improvements in the pipeline, which will also make their way into our future projects.
Examples include:
Additional battery capacity: we believe battery capacity could be increased by at least 40-50% whilst still keeping the total vehicle weight under 1000kg. Major improvements to battery technology were unveiled after our battery packs were assembled, and a redesign of the battery topology to suit would allow for better utilistation of the space within our packs for greater range.
Battery cooling: contrary to internal combustion, cooling in an EV is primarily for when a vehicle is not running but is plugged into an ultra-fast DC charger. The high amperage from these chargers can cause battery cells to heat up, and if they reach a certain level, the car will instruct the charge station to throttle its output. By introducing a battery cooling loop, the car will likely be able to charge at a higher, unthrottled rate.
Drive modes: we hope Future Spec’d vehicles will find use in many varied environments. From the school run, to the track, to a Sunday drive to the pub. To amplify the driving experience we aim to introduce configurable driving modes that dynamically tailor parameters such as regnerative braking, throttle response and acceleration curves based on the driving context. Examples include Sport mode, for increased performance on track, and Eco mode, to optimise for maximum range.
Comfort features: the priorities thus far have been on foundational vehicle and electrical engineering. With a strong architecture now in place, we look forward to introducing some of the invisible and subtle creature comforts found in modern vehicles. We will do so without jeopardising the nostalgia and beauty of the underlying classic car. Examples include air conditioning, cabin heating, seat heating and ventilation, power steering, central locking and GPS tracking.
Art, and musings
Stepping away from the details, our hope for this project was that it would challenge preconceived notions around classic car electrification.
We wanted to show the world that electric cars can be beautiful. That they can be stylish. That they aren’t just for geography teachers and software engineers.
We wanted to throw under the spotlight the incongruity of a nostalgic car from another age, filled to the brim with modern tech, and to have the stubborn and obstinate realise that it’s not such a bad idea after all.
We wanted to challenge thinking and spur discussion.
In essence, this is the objective of art. Art challenges us. Art gets us talking.
Is electrification a new artform? Did this project challenge how you think about classic cars?
Let us know what you think below.
See yourself in an electric 356?
This electric 356 is available for test drives within Australia, by appointment.
Get in touch to explore your own Future Spec’d classic.